Managing and preventing corrosion is the main requirement in many industrial sectors as, for instance, industrial vehicles sector, automotive sector, naval sector, civil and military aeronautics, aerospace sector, or the railway sector. By not correctly dealing with the corrosion issue, people might put at risk not only the product’s performances, but also the safety of the product that the technopolymer lock protects. Continued maintenance, moreover, can negatively burden turnover.
The chemical, or electrochemical, reactions with the environment that can trigger a corrosion process are many and most often are triggered by one of these factors: moisture, temperature extremes, surface liquids, atmospheric dust, salts, industrial lubricants.
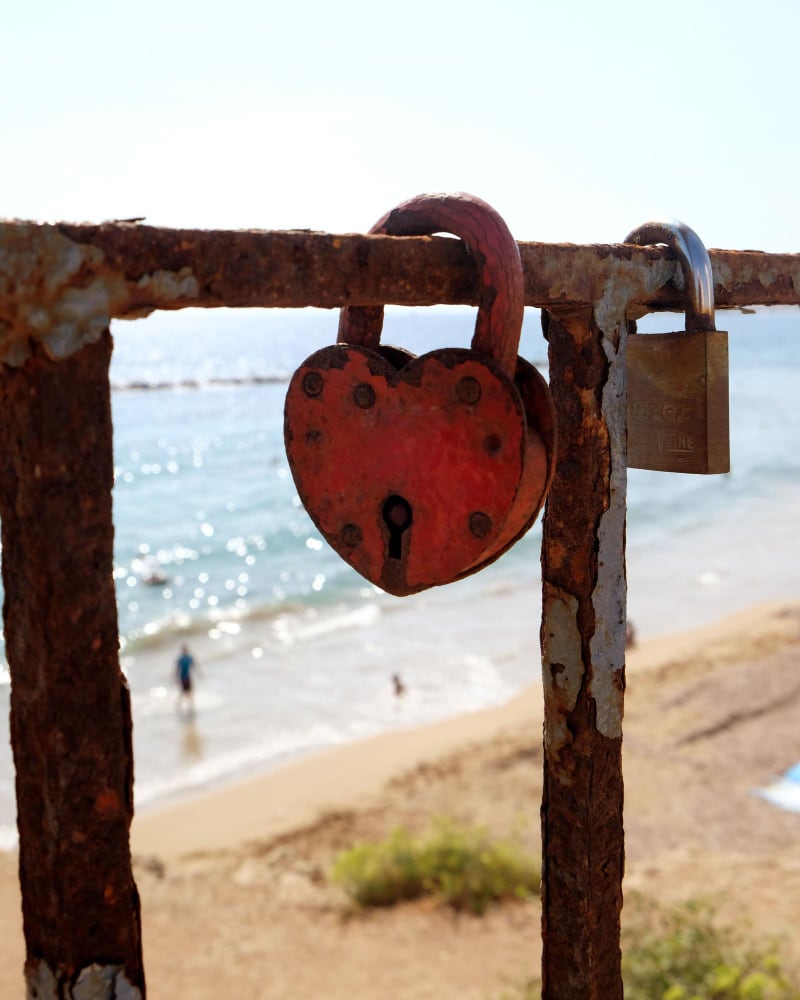
When the going gets tough…
Luckily, thanks to technology, there are plenty of new materials available for project and technical managers to support the production of corrioson resistant products.
Materials make the difference, especially when we talk about products like lock, that are mounted on ships and that must be functional under many different conditions: cold, heat, rain, wind, salt water, corrosion and high mechanical loads. Applications under such conditions require high performances and, for a long time, stainless steel has been the main material for this kind of use. Steel is, by itself, an amazing material that, depending on its different chemical compositions, is divided into four categories: carbon steel, alloy steel, tool steel and stainless steel. The latter does not require protective coatings and is characterized byanti-corrosiveness, resistance against weathering, and seamless integration with its surroundings, earning it unceremoniously the top spot.
However, the advent of nanotechnology, an increasingly tangible reality involving all fields of discipline capable of revolutionizing every field by playing with atoms and molecules, working with objects about one nanometer, one billionth of a meter (10-9m) in size, has brought the advent of truly amazing and innovative materials. Among these we find technopolymers, which are cheaper than machine-worked metal but just as reliable, strong and resistant for many different applications. Recently, technopolymers have even been used, instead of stainless steel, to produce of heart surgery equipment.
Classic and innovative uses of technopolymers
Plastic materials, or polymers, are notoriously used for various engineering projects and in the production of many objects, by injection molding, in many different sectors: electrical, electro-mechanical, electro-chemical, heating, electro-domestic, household appliances, optics, construction, transport, food, industrial automation, medical, personal care. Even in the security and access control industry, lock manufacturing companies use them by making innovative products and making the most of their peculiarities: good or excellent dimensional stability, retention of good mechanical properties even at temperatures above 100°C, ease of processing, high resistance to dynamic loads and aging
The state of the art of special locks – naval, railway and aeronautical sectors
O.M.R. Srl, always observant of innovation and meeting their clients’ needs, has been taking advantage for years of the versatility and innovation of technopolymers in the production of special locks for the naval and railway sector, as well as the aeronautics industry and valve sector. Moreover, thanks to their non-magnetic properties they can be used in furnishings and in the closure of equipment for radiology rooms, thanks to their anti-corrosion properties. They can be used on cleaning trolleys or on cabinets even if in contact with solvents and acids, while, also thanks to the their non-toxic properties, they can be used to close compartments and doors in the food or pharmaceutical sectors. Locks made of technopolymer not only guarantee the same performance as the same steel or zinc alloy models, but are real “chameleons” because, thanks to the various colors, they can perfectly integrate with the product, improving its overall aesthetic appearance.
Moreover, technopolymers are 100% suitable for recycling and avoid the necessary galvanic treatments on steel and zinc alloy, thus reducing the production process and the consequent greenhouse gas emissions, in favor of sustainable production, as required by the 2030 Agenda.
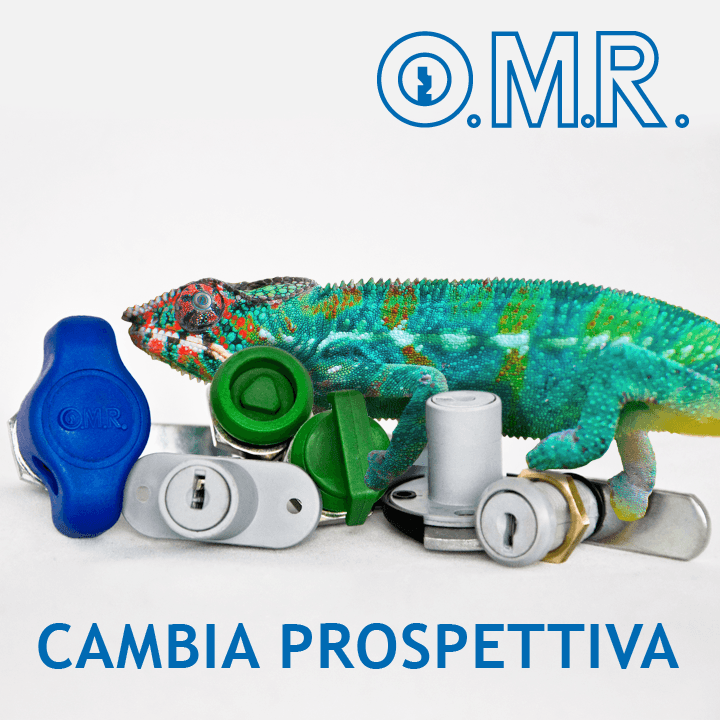
0 Comments